Construction Vehicles - 15 essential heavy machinery types
July 15, 2023
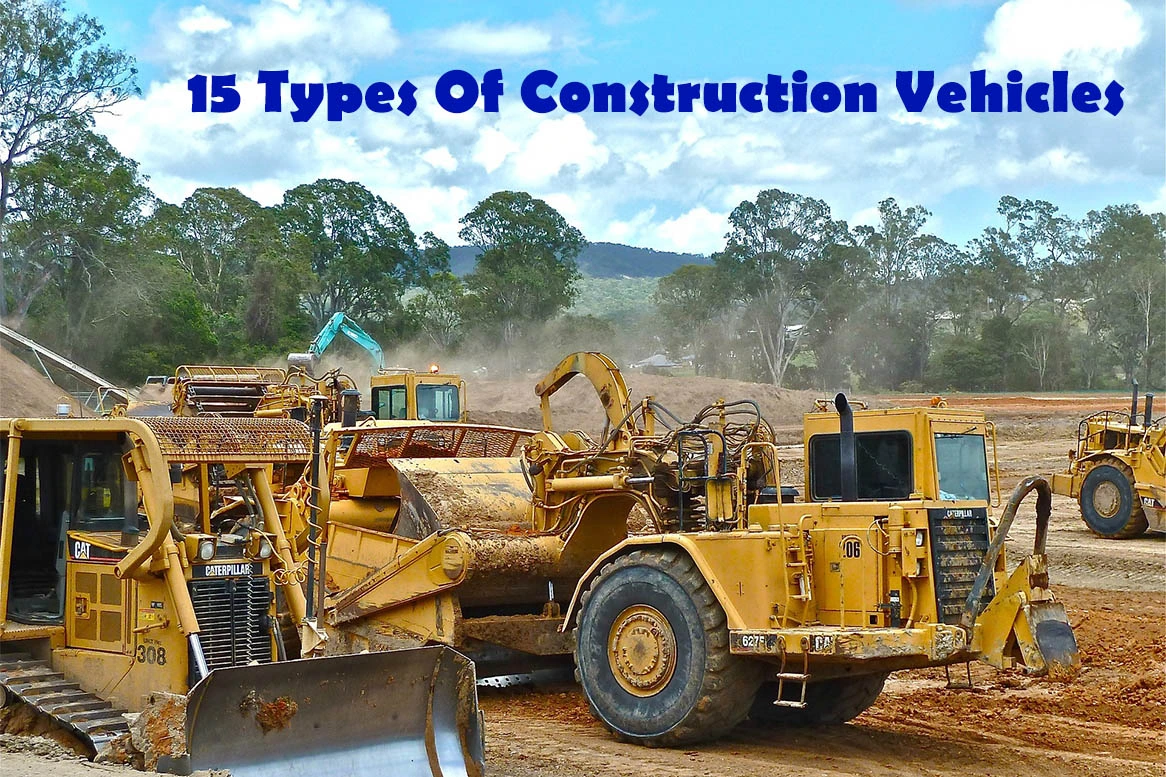
July 15, 2023
Construction vehicles are the epitome of machinery designed to perform heavy-duty tasks on the construction sites. From bulldozers to cranes, these magnificent machines are built to withstand rigorous workloads while seamlessly adapting to a wide variety of tasks. The robust and sophisticated engineering behind these vehicles is impressive, making them capable of lifting and moving massive amounts of earth and materials. From building roads and bridges to constructing buildings, these machines are a crucial component of every construction project, making them some of the most exciting machines we can observe.
1. Excavator: used for digging, lifting, and material handling tasks, excavators have a hydraulic arm with a bucket or other attachments.
2. Bulldozer: equipped with a large blade at the front, bulldozers are used for pushing and leveling soil, debris, or other materials.
3. Loader: these construction vehicles are also known as front loaders or wheel loaders, they are equipped with a bucket at the front for scooping and moving materials.
4. Backhoe loader: a combination of a loader at the front and a small excavator at the rear, backhoe loaders are versatile construction vehicles for digging, loading, and material handling.
5. Grader: these construction equipment with a long blade mounted underneath the machine is used for leveling and grading surfaces, such as roads or building sites.
6. Crane: cranes are used for lifting and moving heavy loads vertically and horizontally. Various types of cranes include mobile cranes, tower cranes, and crawler cranes.
7. Forklift: these most maneuverable vehicles are used for lifting and moving heavy loads on pallets or other materials within construction sites or warehouses.
8. Dump truck: designed for transporting and unloading bulk materials, dump trucks have an open-box bed that can be tilted to unload the contents.
9. Concrete mixer truck: these construction vehicles are equipped with a rotating drum to mix and transport concrete to construction sites.
10. Paver: pavers are used for laying asphalt or concrete surfaces, such as roads or parking lots, with precise thickness and smoothness.
11. Roller: rollers are used to compact soil, asphalt, or other materials to create a stable surface.
12. Scraper: these large machines used for earthmoving tasks, such as cutting, loading, and hauling soil or other materials.
13. Trencher: these construction trucks are used for digging narrow and deep trenches, primarily for installing utility lines or irrigation systems.
14. Aerial lifts: these unique construction vehicles are used for working at heights and providing access to elevated areas during construction or maintenance tasks.
15. Concrete pump truck: these big size trucks are used in the construction industry to transport and place liquid concrete into specific locations, particularly in high-rise or large-scale construction projects.
Discover our collection of construction vehicles toys featuring an array of lifelike replicas of construction trucks and vehicles.
Excavators are powerful construction vehicles designed for a wide range of digging, lifting, and material handling tasks. They consist of a rotating cab, a hydraulic arm with various attachments, and a tracked or wheeled undercarriage. Excavators are commonly used in construction, mining, landscaping, and other industries to perform tasks such as excavation, demolition, and grading.
The main key components of an excavator include: operator cab, hydraulic arm, undercarriage, powerful engine. Excavators can be equipped with different attachments based on the task at hand. Common attachments include buckets for digging or loading materials, hydraulic breakers for demolition work, grapples for handling bulky objects, and augers for drilling holes.
Excavator common applications include: excavation and digging; material handling; demolition; landscaping and grading; road construction; mining and quarrying; pipeline installation; dredging; forestry and logging.
Crawler excavator: also known as tracked excavators, these machines use tracks instead of wheels for enhanced stability and maneuverability, making them suitable for challenging terrains and heavy-duty digging tasks.
Wheeled excavator: wheeled excavators feature wheels instead of tracks, offering increased mobility and faster travel on smooth surfaces. They are often used in urban areas or projects that require frequent relocation.
Mini excavator: compact in size, mini excavators are smaller versions of standard excavators, designed for maneuvering in tight spaces and performing tasks that require precision, such as landscaping, utility work, or residential construction.
Long reach excavator: these excavators have extended hydraulic arms and booms, enabling them to reach further distances and perform deep digging or dredging tasks, commonly used in applications like river or canal maintenance.
Amphibious excavator: these excavators have specially designed undercarriages with floating pontoons or additional attachments that enable them to operate on soft or swampy terrain, such as marshes, wetlands, or shallow water.
Dragline excavator: are massive machines mainly used in mining operations or large-scale civil engineering projects. They feature a large bucket suspended from a boom and cable system, primarily utilized for digging and removing overburden or earth.
A bulldozer is a powerful construction vehicle characterized by its large, heavy frame and a wide, flat blade mounted at the front. It is primarily used for pushing and leveling materials, such as soil, debris, rocks, or snow, during construction, excavation, or land clearing projects.
The main key components of a bulldozer include: operator's cab, hydraulic blade, tracks, rear ripper, engine and counterweight.
Bulldozer common applications include: earthmoving; clearing and leveling; compacting earth; earth braking; mining; snow removal and forestry tasks.
Request your complimentary construction vehicle toy catalog today. Discover an array of exciting options to enhance your child's playtime experience. Do not miss to know fully functional RC bulldozer for kids!
Standard bulldozer: these construction vehicles are the most common type, featuring a wide, straight blade at the front for pushing materials. They are versatile machines suitable for various earth-moving and construction tasks. These vehicles are also often equipped with rear rippers.
Angle blade bulldozer: these vehicles have a blade that can be angled to the left or right. This allows for more precise material control and enables the bulldozer to push materials to the side, making them ideal for tasks like leveling, grading, or backfilling.
U-blade bulldozer: U-blade bulldozers have a U-shaped blade that provides increased capacity for carrying larger volumes of materials. The curved design allows for better material retention and reduces spillage during pushing or carrying operations.
Coal blade bulldozer: Coal blade bulldozers are specifically designed for working in coal mines. They have a specialized blade with additional wear plates and a higher ground clearance to handle the abrasive nature of coal and coal-related materials.
Waste blade bulldozer: Waste blade bulldozers are designed for waste management and landfill operations. They feature a blade with increased capacity and extra guarding to handle the unique requirements of pushing and compacting waste materials.
Swamp or LGP (Low ground pressure) bulldozer: are also known as marsh or wetland bulldozers, are specifically built for operating in soft, wet terrain. They are equipped with wide tracks or additional attachments like swamp shoes to provide better flotation and reduce ground disturbance.
A loader, also known as a front loader or wheel loader, is a heavy construction vehicle commonly used in construction, mining, and other industries. Loader is characterized by its front-mounted bucket or attachment, which is used for scooping, lifting, and transporting materials. Loaders are versatile machines designed to handle a wide range of tasks at construction sites.
The main key components of a loader include: operator's cab, robust chassis, wheels and tires, hydraulic loader arm, articulated joints, engine, bucket or other attachments.
Loader common applications include: loading and unloading construction materials or equipment; handling materials such as soil, gravel, sand etc.; stockpiling materials; construction site cleanups; grading and leveling; snow removal.
Skid steer loader: these construction trucks are compact loaders with a small turning radius, making them ideal for tight spaces and maneuverability. They are equipped with lift arms for attaching various buckets, forks, or other specialized attachments.
Wheel loader: also known as front-end loaders, are large loaders with a front-mounted bucket. They are commonly used in construction, mining, and agricultural industries for material handling, loading trucks, and general-purpose applications.
Tractor loader: are hybrids between tractors and loaders. They are commonly used in agricultural applications for tasks such as loading, hauling, and moving materials on farms or construction sites.
Underground loader: these construction vehicles also known as LHD (Load-Haul-Dump) loaders, are specifically designed for underground mining operations. They are built to operate in confined spaces and harsh conditions, with specialized features for safety and efficiency.
Log loader: these vehicles are designed specifically for handling logs and forestry operations. They are equipped with grapples or clamshell attachments for lifting and moving logs.
A backhoe is a versatile heavy construction vehicle commonly used in construction, excavation, and utility work. It is named for its distinctive feature, a backhoe attachment located at the rear of the machine, which consists of a digging bucket and a hydraulic arm. Most of backhoes are equipped with a front bucket.
The main key components of a backhoe include: operator's cab, chassis, hydraulic backhoe attachment, hydraulic front loader attachment and stabilizers.
Backhoe common applications include: digging and excavating; construction site preparation; utility construction; building materials handling; landscaping and earthmoving; demolition; snow removal.
Standard backhoe: these construction vehicles are the most common type and feature a digging bucket at the rear and a loader bucket at the front.
Mini backhoe: also known as compact backhoes, are smaller-sized machines designed for confined spaces and lighter-duty operations. They offer maneuverability and are often used in landscaping, residential construction, and smaller-scale projects.
Extendable backhoe: also called telescopic backhoes, have a telescoping arm that allows for increased reach and digging depth. They are useful for applications that require extended reach, such as deep excavations or digging in hard-to-reach areas.
Side shift backhoe: these vehicles have the ability to shift the entire backhoe unit to one side. This feature allows for precise digging and working alongside walls or structures without the need for repositioning the entire machine.
Track-mounted backhoe: also known as tracked backhoes, are equipped with tracks instead of tires. This design offers superior traction and stability in challenging terrain conditions such as soft soil, steep slopes, or muddy surfaces.
All-wheel steer backhoe: these construction vehicles provide enhanced maneuverability and agility. They are particularly useful in tight spaces or crowded job sites where precise movements are required.
A grader is one of the essential construction vehicles used to create level and even surfaces on construction sites. It is a highly specialized piece of equipment that features a long blade that can be angled and adjusted to precisely grade surfaces according to the required slope and elevation.
The main key components of a grader include: operator's cab, chassis, wheels and rugged tires, engine and blade.
Grader common applications include: site preparation; landscaping and earthmoving; snow removal.
Motor grader: are one of the most commonly used graders due to their versatility. They are equipped with a long blade that is mounted under the frame, which can be adjusted to different angles for cutting, levelling, and smoothing the ground.
Laser grader: use laser technology to level and shape the ground. They are equipped with a laser receiver that detects the changes in elevation and adjusts the blade accordingly.
Mini grader: these construction trucks are compact and lightweight, making them ideal for smaller projects or areas with limited access. They are equipped with a smaller blade and offer better maneuverability, making them suitable for tasks such as landscaping, snow removal, and driveway maintenance.
Articulated grader: are equipped with an articulated frame, which allows for better maneuverability and control. They are mostly used for tasks such as forestry, mining, and quarrying, where there is a need for increased maneuverability.
Maintainer grader: are designed for rough terrain and extreme weather conditions. They are equipped with a ripper attachment that can be used to break up tough ground, making them ideal for land preparation in areas with rocky, uneven terrain.
Cranes are an essential piece of equipment used in a wide range of industries to lift and move heavy loads safely and efficiently. These highly versatile machines can be found on construction sites, in manufacturing facilities, ports, and transportation hubs.
The main key components of a crane include: operator's cab, base made of concrete and steel, mast (tower), jib (horizontal arm), counter-jib, slewing mechanism (gearbox that can safely hold weights), hoist (mechanism to lower and raise loads).
Crane common applications include: construction sites, shipping and ports; manufacture facilities, logistics and warehousing, power plants and refineries, mining.
Tower Crane: these are fixed cranes commonly used in the construction of tall buildings and structures. They have a vertical mast or tower and a rotating jib with a lifting capacity that can reach hundreds of meters.
Mobile crane: are mounted on wheeled or tracked vehicles and can have various configurations, such as telescopic or lattice booms. Mobile cranes are used in construction, infrastructure projects, and other applications requiring mobility.
Crawler crane: heavy-duty cranes mounted on crawler tracks. They provide stability and excellent lifting capacity on rough or uneven terrain. Crawler cranes are commonly used in construction, bridge-building, and heavy lifting operations.
Gantry crane: are similar to overhead cranes but are supported by a gantry structure instead of being suspended from a building's ceiling. They are used in ports, shipyards, and manufacturing facilities for lifting and moving heavy loads.
Overhead crane: also known as bridge cranes, are fixed cranes that run along tracks mounted on the ceiling of a building or structure. They are commonly used in factories, warehouses, and industrial settings to lift and move heavy materials and equipment.
Jib crane: consist of a horizontal arm, or jib, that is mounted on a vertical mast or wall. They are commonly used in workshops, manufacturing plants, and loading docks for localized lifting and maneuvering of loads.
Rough terrain crane: are specifically designed for off-road applications and uneven surfaces. They feature sturdy, all-terrain tires, and their compact design allows them to maneuver in tight spaces. These cranes are commonly used in construction sites, oil fields, and infrastructure projects.
Floating Crane: are mounted on barges or pontoons and are used for marine construction projects, port operations, and salvage operations. They provide lifting capabilities in water bodies where conventional cranes cannot operate.
Telescopic crane: have a boom that consists of several nested sections that can extend or retract, allowing for various lifting heights and reach. They are commonly used in construction, maintenance, and utility work.
Loader crane: also known as knuckle boom cranes, are typically mounted on trucks or trailers. They feature multiple articulated sections that can fold and unfold like a knuckle, making them suitable for loading and unloading goods in various industries.
A forklift, also known as a lift truck or a powered industrial truck, is a versatile and commonly used piece of material handling equipment in warehouses, distribution centers, and other industrial settings. Forklifts are designed to lift, move, and stack heavy loads.
The main key components of a forklift include: operator's cab, chassis, engine or battery, hydraulic mast (vertical assembly to support forks), forks, counterweight, tires.
Forklift common applications include: warehouse operations, freight handling, construction sites, manufacturing facilities, farming, recycling.
Counterbalance forklift: are the most common type of forklifts used in warehouses and industrial settings. They have a weight at the rear of the truck that counterbalances the load being lifted, eliminating the need for outriggers or additional support.
Reach forklift: are designed for narrow aisle operations. They have telescopic forks that can extend forward to reach loads stored on racks or shelves. Reach forklifts are ideal for maximizing vertical storage space in warehouses.
Order picker: are used primarily in fulfillment centers and distribution warehouses. They have a platform that allows the operator to be elevated along with the forks, enabling them to pick individual items from high shelves or racks.
Pallet jack: known as pallet trucks, are manual or electric-powered devices used to move pallets on flat surfaces. They have forks that can be lowered to slide under pallets, allowing for easy maneuverability and transport.
Rough terrain forklift: are designed for outdoor use on uneven or unpaved surfaces. They are equipped with large, rugged tires and have a higher ground clearance, providing better traction and stability in rough terrain conditions.
Industrial forklift: are heavy-duty forklifts with higher lifting capacities. They are used in demanding industrial environments such as steel mills, lumber yards, and construction sites where large and heavy loads need to be handled.
Side Loader: are designed to load and unload long or wide loads from the side. They have forks mounted on the side of the truck and are commonly used for handling items such as lumber, pipes, and sheet materials.
Telescopic handler: also known as telehandlers, are versatile machines combining the features of a forklift and a crane. They have a telescopic boom that can extend forward and upward, allowing for lifting and placing loads at various heights and distances.
Articulated forklift: also called multi-directional forklifts, are designed for maneuverability in tight spaces. They have a unique articulated chassis that enables them to move in multiple directions, making them ideal for handling long and bulky loads in narrow aisles.
A dump truck, also known as a tipper truck or dumper, is a heavy-duty vehicle designed for transporting loose materials such as sand, gravel, soil, or construction debris. It is commonly used in construction, mining, and other industries where large quantities of material need to be moved. Dump trucks are characterized by their open-box bed, which is hinged at the rear and equipped with hydraulic rams.
The main key components of a dump truck include: driver's cab, bed (dump body), hydraulic tipping mechanism, chassis, engine, wheels and suspension.
Dump truck common applications include: construction sites, mining and quarrying, waste management, agriculture and landscaping, road maintenance, demolition work.
Standard dump truck: this is the most basic type of dump truck, featuring a truck chassis with a dump body mounted on the frame. It typically has a hydraulic piston or cylinder that lifts the front of the dump body to unload the materials.
Articulated dump truck: also known as an ADT, this type of dump truck consists of a cab and a trailer-like dump body that is attached with a pivot joint. The articulation allows for increased maneuverability on rough terrains, making it popular in construction, mining, and off-road applications.
Transfer dump truck: or "slinger," has a separate trailer that can be loaded independently of the truck. The trailer is connected to the truck by a hydraulic arm or conveyor belt system, enabling the materials to be transferred and unloaded quickly. This type of truck is useful for delivering materials to multiple locations without returning to a central point for reloading.
Side dump truck: feature a hydraulic tilting mechanism that allows the dump body to tilt to either side, enabling the materials to be discharged to the left or right of the truck. Side dump trucks are often used for dumping on the move, making them suitable for certain construction, mining, and agricultural applications.
Semi-trailer dump truck: this type of dump truck consists of a tractor unit and a separate trailer with a dump body. The trailer is connected to the tractor via a fifth wheel coupling. Semi-trailer dump trucks offer increased hauling capacity and are commonly used for long-distance transportation of materials.
Bottom dump truck: have a clamshell-type dump body that opens from the bottom, allowing the materials to be discharged in a controlled manner. This design is advantageous when working in tight spaces or when precise spreading of materials is required, such as in road construction or agricultural applications.
Haul truck: are massive dump trucks primarily used in large-scale mining operations. They are designed to carry extremely heavy loads of minerals or overburden (material covering the valuable mineral deposits). Haul trucks are often among the largest and most powerful dump trucks, capable of transporting several hundred tons of material.
A cement mixer truck, also known as concrete mixer truck, is a specialized vehicle designed for the transportation and mixing of concrete at construction sites. It is an essential component in the process of delivering freshly mixed concrete from the batching plant to the construction location.
The main key components of a cement mixer truck include: driver's cab, drum, mixing system, water supply system, chassis, control system, discharge chute.
Cement mixer truck common applications include: concrete delivery and on site cement mixing.
Standard transit mixer: this is the most common type of cement mixer truck. It features a rotating drum mounted on the back of a truck chassis. The drum has blades or fins inside for mixing the concrete during transportation. Standard transit mixers come in various sizes, ranging from small to large, with capacities typically measured in cubic meters or cubic yards.
Volumetric mixer truck: also known as mobile batch plants or on-site mixers, are versatile units that can produce concrete on-demand. They have separate compartments for storing the raw materials (cement, aggregates, water) and mix them together as needed. Volumetric mixer trucks allow for precise control over the concrete mixture, making them ideal for projects with specific mix design requirements or where multiple types of concrete are needed.
Self-loading mixer truck: combine the functions of a cement mixer truck and a front-end loader. They have a self-contained mixing system and a bucket or shovel at the front that can load raw materials (aggregates, cement, water) directly into the mixing drum. This type of mixer truck is convenient for smaller projects or locations where a separate loader may not be readily available.
Mini mixer truck: are smaller-sized cement mixer trucks, designed for narrow or restricted access construction sites. They have reduced dimensions and capacities compared to standard transit mixers, making them suitable for projects with space limitations or lighter concrete requirements.
Off-road mixer truck: are specifically designed for rough terrains or off-road construction sites. They feature enhanced suspension systems, larger tires or trucks, and robust chassis to navigate challenging environments. These trucks are commonly used in mining operations, remote construction sites, or projects that require concrete delivery in difficult-to-reach areas.
Trailer-mounted mixer: consist of a mixer drum mounted on a trailer, which can be towed by a truck or other vehicle. They offer flexibility in terms of transportation and can be easily moved between construction sites. Trailer-mounted mixers are commonly used for smaller projects or in situations where frequent relocation is required.
A construction paver, also known as an asphalt paver or a concrete paver, is a heavy-duty machine used in road construction and paving projects. It is designed to lay asphalt or concrete surfaces with precision and efficiency.
The main key components of a paver include: operator's cab or control panel, hopper (holds asphalt and concrete mixture), screed (responsible for leveling and shaping asphalt or concrete), augers (helps to distribute asphalt or concrete evenly), compaction system (not all pavers are equipped with it), tracks or wheels.
Paver common applications include: road constructions, parking lots constructions, airport runways constructions, sidewalks and walkways.
Asphalt paver: they are available in a wide range of sizes, shapes, colors, and surface finishes. Asphalt pavers offer versatility and durability, making them suitable for various applications, including roads, driveways, walkways, and patios.
Track paver: have tracks instead of wheels, providing excellent traction and stability on uneven surfaces. They are commonly used in large-scale road construction projects.
Wheeled paver: have rubber tires and are ideal for paving smaller roads, parking lots, or residential driveways. They offer good maneuverability and can easily move around tight corners.
Slipform paver: are used for continuous, automated concrete paving. They have a mechanism that forms the concrete into the desired shape while moving forward. These pavers are often used for highway construction and large concrete paving projects.
A construction roller, also known as a road roller or steamroller, is a heavy-duty construction vehicle used for compacting roads, pavements, and other types of groundwork. It is an essential machine in the construction and maintenance of highways, airports and parking lots.
The main key components of a roller include: operator's cabin, chassis, roller drum, engine, water system and vibratory (oscillation) system.
Roller common applications include: road constructions; ground foundation preparation; airport runways; parking lots; sports fields.
Smooth drum roller: this type of roller has a smooth steel drum without any protrusions. Smooth drum rollers are effective for compacting granular materials like soil, gravel, and asphalt. They provide uniform compaction and are commonly used in road construction and large-scale compaction projects.
Padfoot roller: also known as a sheepsfoot roller, a padfoot roller has a drum with round or rectangular protrusions, resembling the feet of a sheep. These protrusions, called pads or lugs, provide concentrated pressure and are ideal for compacting cohesive soils like clay. Padfoot rollers are commonly used in trench backfilling, landfill construction, and compacting cohesive or semi-cohesive soils.
Pneumatic roller: have rubber tires instead of a steel drum. These rollers are filled with air, and the tires provide pressure and compaction. Pneumatic rollers are used for compacting asphalt layers, particularly in areas where gentle compaction is required or where the surface needs to be sealed and finished.
Vibratory roller: have a vibrating drum that generates high-frequency vibrations. These vibrations enhance the compaction process, increasing the density of the material being compacted. Vibratory rollers are effective for compacting granular materials and are commonly used in road construction, parking lots, and other applications where high compaction is desired.
Combination roller: also known as combination rollers, are versatile machines that combine the functions of both a smooth drum roller and a pneumatic roller. These rollers have both a smooth steel drum and rubber tires, allowing them to perform both static and vibratory compaction. Combination rollers are used in various applications, providing flexibility for different types of materials and surface conditions.
Walk-behind roller: are smaller-sized rollers that can be operated manually. They are commonly used for compacting smaller areas, such as driveways, footpaths, and landscaping projects. Walk-behind rollers are available in various configurations, including smooth drum, padfoot, and vibratory options.
Trench roller: are compact rollers specifically designed for compacting soil in narrow trenches or confined spaces. They are characterized by their compact size, maneuverability, and often feature an articulated or segmented drum to better adapt to the trench shape. Many of this construction vehicles are are remotely operated via radio.
Scraper vehicles are known for their high productivity and efficiency in bulk earthmoving operations. They can handle large volumes of material in a relatively short time, making them ideal for projects that require extensive excavation or leveling. They are also designed for easy maneuverability, often featuring articulated steering systems that enhance their mobility on rough or uneven terrain.
The main key components of a scraper include: operator's cabin, chassis, bowl (responsible for collecting and storing the material), blade, engine,
Scraper common applications include: excavation and leveling; transportation; landscaping; material spreading and compacting; mining operations.
Tractor scraper: these are the most basic and widely used scrapers. They consist of a single bowl attached to a tractor unit. Traditional scrapers are versatile and suitable for a range of earthmoving tasks.
Elevating scraper: have a similar design to traditional scrapers but include a hydraulic system that allows the bowl to be raised and emptied without tilting or ejecting the material. This feature enables more precise control of material discharge and reduces the need for additional equipment, such as dozers, for spreading the material.
Open bowl scraper: have a flat or shallow bowl design without a cutting edge. They are commonly used for moving loose materials, such as sand, gravel, or topsoil, over shorter distances. Open bowl scrapers are particularly efficient for spreading and leveling operations.
Coal bowl scraper: are specifically designed for mining operations involving the extraction and hauling of coal or other bulk materials. Coal bowl scrapers have high-capacity bowls with special linings or coatings to withstand the abrasive nature of coal and prevent damage.
Push-pull scraper: consist of two scrapers connected in tandem, working together to increase the hauling capacity. The front scraper cuts and loads the material into its bowl, while the rear scraper pushes the material forward into its own bowl. This configuration allows for increased productivity and efficiency in earthmoving tasks.
Ejector scraper: feature a push plate or ejector mechanism at the back of the bowl. Ejector scrapers are often pulled by tractors or other heavy construction trucks.
A trencher is a specialized construction machine used for digging trenches in the ground. Trenchers are designed to perform trenching tasks quickly and efficiently, replacing manual digging methods.
The main key components of a trencher include: operator's cabin, chassis, conveyor system to remove excavated material, hydraulic boom, trenching attachment - digging chain or cutting teeth.
Trencher common applications include: install underground utilities - cables, pipelines, sewers etc.; landscaping and irrigation; agriculture and farming; road infrastructure construction.
Chain trencher: also known as bucket wheel trenchers or ladder trenchers, are the most common and versatile type of trenchers. They use a digging chain fitted with cutting teeth or buckets to excavate the soil and create trenches. Chain trenchers can handle a wide range of soil conditions and trenching widths, making them suitable for various applications.
Wheel trencher: feature a large digging wheel with cutting teeth or blades mounted on the side of the machine. The wheel rotates and cuts into the soil, creating the trench. Wheel trenchers are generally used for shallow trenches and can be effective in sandy or softer soil conditions.
Mini trencher: are designed for creating narrow and shallow trenches, typically for the installation of fiber optic cables or small-diameter utility lines. They are compact machines that utilize a specialized cutting attachment to cut a thin trench while minimizing disruption to the surrounding area.
Rock wheel trencher: also known as rock saws or rock trenchers, are specifically designed for cutting through hard or rocky terrain. They feature a rotating cutting wheel with carbide-tipped or diamond-coated teeth that can effectively cut through challenging ground conditions.
Vibratory plow trencher: utilize a vibrating blade or plow to create shallow trenches by displacing the soil rather than removing it. They are commonly used for installing irrigation lines, cables, or smaller-diameter utility lines in softer or loamy soil conditions.
A construction aerial lift, also known as an aerial work platform or aerial lift equipment, is a versatile machine used in construction, maintenance, and other industries to provide temporary access to elevated areas. It allows workers to perform tasks at height safely and efficiently. Aerial lifts are designed to lift personnel, tools, and equipment to elevated work locations, offering a stable and secure platform.
The main key components of an aerial lift include: operator's cab or control panel, boom or scissors lift, platform, outriggers or stabilizers.
Aerial lift common applications include: maintenance and construction; tree care; telecommunications; warehousing; filming.
Scissor lift: are versatile and commonly used aerial lifts. They feature a platform that moves vertically using a scissor-like mechanism. Scissor lifts are ideal for tasks that require straight vertical movement, such as maintenance, installation, and construction work.
Boom lift: also known as cherry pickers, feature a hydraulic arm (boom) with a platform attached at the end. This arm can extend and articulate, allowing workers to reach heights and positions that are difficult to access with other types of lifts. Boom lifts are commonly used in construction, maintenance, and firefighting operations.
Personnel lift: also called personnel hoists or man lifts, are designed specifically for lifting individuals to elevated areas. These lifts have a small platform or a bucket with guardrails, allowing workers to perform tasks at moderate heights. Personnel lifts are often used in tasks such as inventory management, inspection, and maintenance work.
Articulating lift: also known as knuckle lifts, have multiple boom sections that can articulate or bend, allowing for more flexibility in reaching around obstacles or accessing difficult areas. These lifts are commonly used in construction, painting, and maintenance tasks where precise positioning is required.
Telescopic lift: also called straight or stick lifts, have a straight, extendable boom that can reach great heights. They offer high vertical and horizontal reach, making them suitable for tasks such as construction, maintenance, and utility work.
Trailer-Mounted Lift: these lifts are mounted on a trailer for easy transportation. They can be towed behind a vehicle and are commonly used for short-term projects or in locations where frequent movement is required.
Spider lift: also known as tracked aerial lifts, feature articulated booms mounted on spider-like legs or tracks. They are highly maneuverable and can operate on rough or uneven terrain, making them suitable for tasks such as tree care, landscaping, and maintenance in challenging environments.
A concrete pump truck, also known as a concrete boom pump, is a specialized vehicle used in construction projects to transport and distribute concrete to specific locations. Unlike a concrete mixer truck, which primarily transports concrete, a concrete pump truck is designed to pump concrete directly from the truck-mounted pump to the desired location.
The main key components of a concrete pump truck include: pumping system, boom assembly, delivery hose or pipe, stabilizers, control system.
Concrete pump truck common applications include: high rise construction projects; hard to reach areas (behind obstacles or narrow spaces).
Boom pump: are the most commonly used type of concrete pump trucks. They feature a hydraulic boom with multiple sections that can be extended and maneuvered to reach various heights and distances. Boom pumps are suitable for large-scale projects, high-rise construction, and precise concrete placement.
Line pump: also known as trailer-mounted concrete pumps, are compact and versatile. They are mounted on a trailer or skid and are ideal for smaller construction sites or projects that require concrete to be pumped over shorter distances. Line pumps are often used for residential construction, floor slabs, and repairs.
Separate placing boom: consist of a separate, self-supporting boom that is mounted on a stationary base or a separate structure. These pumps are commonly used in applications where the boom needs to be permanently installed, such as large construction projects, bridges, and tunnels.
City pump: also called truck-mounted stationary pumps, are compact and highly maneuverable. They are designed for urban construction sites with limited space and tight access. City pumps can be mounted on a truck chassis or a trailer and are suitable for small to medium-sized projects, including building renovations and urban infrastructure work.
High-pressure pump: are specifically designed for projects that require the pumping of concrete over long distances or to higher elevations. These pumps are capable of delivering concrete with high pressure, enabling efficient pumping over extended pipelines.
Squeeze pump: also known as peristaltic pumps, operate by squeezing a flexible tube to move the concrete through the pumping system. They are commonly used for pumping specialized concrete mixes, such as shotcrete or low-slump concrete, where maintaining the mix integrity is crucial.
Double E Hobby RC construction vehicles manufacturer
At Double E Hobby, we take pride in our production of top-quality RC construction equipment. Our selection includes a range of Volvo RC excavators and trucks, all made available to you since 2019. Experience industry-leading performance and precision in your hobbyist pursuits with our reliable and high-performing models. Double E is also a manufacturer of toys.